Modern industry and construction have seen the emergence of several effective, adaptable, and long-lasting mechanical equipment due to the constant improvement of technology and the variety of demands. Of them, the light steel frame machine, or LGS machine, is gaining market favor and attention as a cutting edge piece of equipment that combines automated building, material processing, and structural design. This article will thoroughly examine the definition, traits, benefits, and uses of LGS machines across a range of industries.
What is LGS machine?
The light steel frame machine, also known as the LGS machine, is a piece of mechanical equipment specifically designed for the fabrication, assembly, and installation of light steel structures. It combines many procedures, including punching, welding, shaping, and cutting steel, into a single step, resulting in great automation, efficiency, and accuracy in the creation of steel structures. The original goal of the LGS machine’s design was to minimize production costs and enhance overall engineering quality by streamlining production procedures, maximizing material utilization, and minimizing manual intervention. It also aimed to satisfy the demands of contemporary industrial and construction fields for lightweight, quick, and environmentally friendly steel structures.
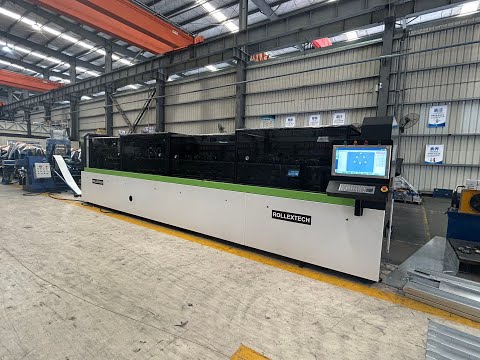
The LGS machine’s features
- High efficiency: The LGS machine uses an automated production process that allows it to continually cut steel, mold steel, weld steel, and perform other tasks. This significantly increases the efficiency of manufacturing. Its sophisticated control system can precisely regulate production parameters at the same time to guarantee consistent and dependable product quality.
- High precision: LGS machines can precisely process and assemble steel thanks to their exact mechanical structure and cutting-edge sensing technology, fulfilling the stringent standards for structural correctness in the industrial and construction sectors.
- Flexibility: LGS machines are highly adaptive and may be readily modified to meet various production requirements. It can readily handle the fabrication of both basic steel frame structures and sophisticated steel structure components.
- Protection of the environment: LGS machines can efficiently cut down on energy and material waste during production, as well as noise and dust pollution. They can also align with the green production philosophy of contemporary industry.
Key components of light steel keel machine
1. Basic components of machine tools
The fuselage, also known as the machine tool body, serves as the equipment’s supporting structure and must be sufficiently robust to provide stable operation, transit, and installation.
In order to provide a strong basis for the equipment’s functional implementation, the fuselage design must guarantee the flatness and horizontality of the installation components.
2. Forming module and archway
Archway (wall panel): Made in accordance with the forming module, this component set includes sliders, forming molds, spindles, bearings, and other parts that work together to produce a whole process.
The primary force direction in manufacturing, which guarantees the precision and stability of material formation, is the vertical position of the archway.
The various forming module designs—9 passes, 12 passes, etc.—are chosen based on particular requirements.
Mold: The precision and look of the product are directly impacted by the quality of the mold. In order to guarantee that the molds used in light steel keel machines are non-deformed, wear-resistant, and have a high quality, they are often heat-treated, finely processed, and plated.
3. Power supply system
The main purpose of a hydraulic system is to power essential parts like fixed-length shearing molds and stamping molds.
For system functioning to be stable and reliable, hydraulic power needs the assistance of hydraulic pumps.
Drive system: In charge of creating the equipment’s transmission, including servo gear, sprocket transmission, etc.
The drive system ensures that the processing process proceeds smoothly by producing a consistent power output.
IV. Transmission and control components
Transmission parts: These include ball screws, gear transmissions, and other parts that guarantee the equipment’s parts operate in unison.
Precision transmission parts contribute to increased manufacturing efficiency and processing accuracy.
Control system: Including the integration of many systems, such as manufacturing, design, and electronic control systems.
In order to guarantee the precision and stability of the processing process, the equipment must be monitored and operated overall by the control system.
V. Other key components
Motor and oil pump: The equipment, including the 4 kW reducer that powers the forming module, is primarily powered by the motor.
In order to maintain the hydraulic system’s proper functioning, the oil pump serves as the power source.
Shearing device: To precisely shear light steel keel materials, for instance, a shearing device with a cy12mov blade quenching is used.
Fasteners and accessories:
such as joints, expansion bolts, hangers, and other accessories that are utilized to attach and fasten the ceiling system and keel frame.
The stability and safety of the product are also closely correlated with the caliber and choice of these accessories.
How to run a machine made of light steel
1. Preparation stage
- Safety check: Make sure that all pieces of the light steel machine are securely fastened together, that the safety measures are dependable and functional, and that the machine’s equipment is in good condition before starting it up.
- Environmental preparation: Clear the workspace of any trash and make sure that nothing combustible or explosive is present. Then, set up the necessary instruments, auxiliary equipment, and raw materials.
- Inspection before to startup: Verify that the machine is in standby mode and that no unusual warning information is present. You should also check the stability and dependability of the power supply, gas source, and other power sources.
2. Turn on the device
- Start the power supply: Connect the power supply appropriately and flip on the appropriate power switch in accordance with the instructions provided in the machine handbook.
- Turn on the machine: To turn on the light steel machine, press the start button. Keep an eye on the machine’s performance throughout the starting phase to make sure there are no unusual noises, vibrations, or odors.
3. Modify the settings
- Establish processing parameters: Modify the light steel machine’s processing settings, such as cutting length, angle, speed, etc., based on production requirements. Verify the accuracy of the parameter settings.
- Equipment debugging: Perform a no-load test run to verify that the processing accuracy and stability satisfy specifications and that every part of the machine operates in a coordinated and consistent manner.
4. Get the processes going
- Loading: Position the machine’s light steel material to be processed at the designated spot and secure it.
- Start the processing program: In order for the light steel machine to carry out cutting, shaping, and other processing operations in accordance with the predetermined trajectory, start the processing program via the control panel or computer program.
- Watch the processing process: Throughout the process, keep a careful eye on the machine’s operational state and processing quality. Adjust settings or respond quickly to any unusual circumstances.
5. Final processing
Press the stop button in time to bring the light steel machine to a halt when the processing work is finished.
Unloading: Take out the machine’s processed light steel products and do a quick quality check.
Site cleanup: Tidy up the workspace, gather trash, recyclables, and other detritus, and maintain a clean atmosphere.
6. Maintenance and shutdown
Switch off the power: Unplug the power plug and flip off the power switch after making sure the computer has stopped operating entirely.
Daily upkeep: Follow the guidelines in the machine handbook for daily upkeep and repairs, including wiping down the machine’s exterior, monitoring the oil level, changing worn-out components, etc.
For further analysis and improvement, be sure to document all pertinent information about this operation, including processing time, amount, quality, etc.
Advantages of LGS machines
- Cut expenses: By carefully regulating production parameters, automated manufacturing not only increases material utilization but also lowers the cost of raw materials. It also decreases labor dependency and labor costs.
- Enhance quality: Human error-related quality issues are minimized by the high-precision processing and assembly capabilities of LGS machines, which guarantee the steady and dependable quality of steel structures.
- Reduce construction time: LGS machines’ high production efficiency allows them to produce and install a lot of steel structures quickly, which cuts down on the amount of time needed to finish the project’s construction.
- Increased safety: Buildings and industrial facilities may benefit from the strong bearing capacity and stability of the steel structures produced by LGS machines.
Application fields of LGS machines
In several industries, including construction, bridges, tunnels, manufacturing facilities, stadiums, exhibition spaces, etc., LGS machines are extensively used. In the industrial sector, it is used to manufacture different equipment brackets, pipe brackets, platforms, and other steel structure components. In the building industry, it is primarily used to make various kinds of steel structure frames, roof systems, wall systems, etc. Furthermore, as modular and prefabricated structures become more popular, LGS machines are becoming more and more crucial to the manufacture and installation of prefabricated steel structural components.
Conclusion
Light steel frame machines, or LGS machines for short, have shown enormous promise and value in the fields of contemporary industry and construction because to their high levels of environmental protection, flexibility, efficiency, and accuracy. With technology developing at a rapid pace and the market growing, LGS machines will undoubtedly become more significant in a variety of industries and help the industry move toward greater efficiency, sustainability, and environmental friendliness.