High pressure polyurethane Sandwich Panel Line, sandwich panel foaming line is a special equipment used to produce polyester high-pressure foam roof panels. The panel has a lot of advantages like lightweight and durable roofing sheets with excellent thermal insulation properties
An industrial equipment production line created expressly for the purpose of creating polyester foam is the high-pressure polyester foam production line. Using high-pressure technology, it mixes liquid polyester material with other additives and sprays the combination onto the surface that needs to be coated or filled in a certain way. It then starts to foam when it comes into contact with air, finally developing into a sturdy polyester foam.
A vast variety of construction industries, including cold storage, hospitals, stadiums, cars, villas, and upscale buildings, heavily rely on high pressure polyurethane panels. The performance of our PU line is comparable to that of similar goods sold both locally and abroad.
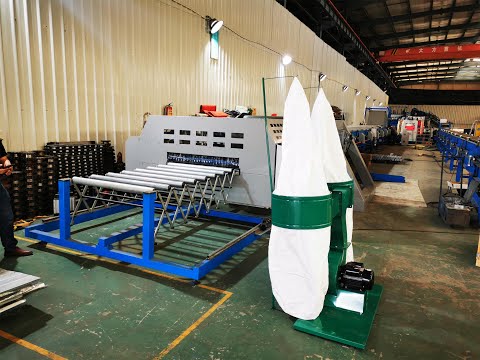
Polyurethane board machine specifications
A machine specifically designed for producing polyurethane roof panels is called a polyurethane board machine, or polyester high-pressure foam roof panel manufacturing line. It creates lightweight, long-lasting roof panels with exceptional thermal insulation performance by fusing high-pressure foaming technology with the special qualities of polyester materials.
Main components of the production line:
- In order to maintain the stability and continuity of the manufacturing process, liquid polyester ingredients and other additives needed for the creation of polyurethane boards are stored in a raw material storage system.
- High-pressure foaming system: The liquid polyester material and other additives are combined and foamed to create a homogeneous and thick foam structure by carefully regulating the pressure, temperature, and mixing ratio.
- Molding system: The foamed mixture is molded precisely in the molding system to guarantee that every roof panel satisfies the predetermined dimensions and forms.
- Cutting and packaging system: The cutting system perfectly cuts the molded roof panels, and the packaging system neatly packages them for convenient storage and transit.
Product features:
Because of its outstanding thermal insulation performance, durability, and light weight, polyurethane boards are frequently employed in the building sector. In order to provide buildings complete thermal insulation solutions, it may be utilized as external wall ornamental panels, wall sound insulation panels, roof insulation panels, etc. Because of its superior thermal insulation capabilities, buildings use less energy and are more energy-efficient.
Detailed explanation of machine components
Two well-designed hydraulic unwinders, each capable of supporting a 5 ton weight, are attached to a movable trolley to facilitate the effortless unwinding of coils of raw materials. The movable trolley with equipment not only boosts operational flexibility but also significantly enhances productivity.
Dual roll forming machines: An essential piece of machinery on the manufacturing line are these two roll forming machines. The raw components are transformed into polyurethane boards with predetermined sizes and forms using a precision rolling process. The equipment’s steady functioning guarantees the items’ excellent quality and uniformity.
A high-pressure polyurethane foaming machine is the main tool used in the manufacture of polyurethane boards. To make sure the liquid polyester material is thoroughly combined and foams with other additives, high-pressure technology is used. Its self-cleaning system’s nozzle head successfully avoids blockages and guarantees the stability and continuation of output.
Host: In charge of directing and coordinating the actions of every part on the production line, the host serves as its central control unit. It incorporates sensor technologies and sophisticated control algorithms to guarantee the stability and effectiveness of the whole manufacturing process.
PLC control system: The manufacturing line is powerfully managed and controlled by the sophisticated PLC control system. Operators may simply establish settings, check operational status, and achieve automated production using an easy-to-use operation interface.
Servo motor cutting system: Accurate cutting of polyurethane panels is ensured by the cutting system’s high-precision servo motors. The system can cut materials of various sizes and requirements quickly, accurately, and steadily.
Example and project images: